Designers and motor personnel advantage from discovering a supplier that's an skilled resource of info to assist in pragmatic motor choice. Involve application specialists as early as you possibly can, as they are able to assist create prototypes, custom electrical and mechanical styles, mountings, and gearboxes. This also reduces expenses related with shorter lead occasions and rush delivery.
Servo motors can offer higher performance, faster speeds, and smaller sizes. PM synchronous motors offer advantages on high-energy- consuming and high-dynamic applications, compared to induction motors. Variable frequency drives used with asynchronous motors also can be used with synchronous servo motors, producing higher efficiencies than an asynchronous motor, using perhaps 30% less energy in positioning applications.
Induction motor systems (lower cost, rugged, reliable, and well known) can offer an alternative to servo motor systems (the traditional, established solution) for certain applications. This, of course, is based on similar electronic controls being used (with the latest technology and approximately the same cost), leaving the cost of motors the differentiating issue.
Overview of the pros and cons of each motor type
Induction motor
SPEED - Less speed range than PMAC motors • Speed range is a function of the drive being used — to 1,000:1 with an encoder, 120:1 under field-oriented control
EFFICIENCY - Even NEMA-premium efficiency units exhibit degraded efficiencies at low load
RELIABILITY - Waste heat is capable of degrading insulation essential to motor operation • Years of service common with proper operation
POWER DENSITY - Induction produced by squirrel cage rotor inherently limits power density
ACCURACY - Flux vector and field-oriented control allows for some of accuracy of servos
COST - Relatively modest initial cost; higher operating costs
PMAC
SPEED - VFD-driven PMAC motors can be used in nearly all induction-motor and some servo applications • Typical servomotor application speed — to 10,000 rpm — is out of PMAC motor range.
EFFICIENCY - More efficient than induction motors, so run more coolly under the same load conditions
RELIABILITY - Lower operating temperatures reduces wear and tear, maintenance • Extends bearing and insulation life • Robust construction for years of trouble-free operation in harsh environments
POWER DENSITY - Rare-earth permanent magnets produce more flux (and resultant torque) for their physical size than induction types
ACCURACY - Without feedback, can be difficult to locate and position to the pinpoint accuracy of servomotors
COST - Exhibit higher efficiency, so their energy use is smaller and full return on their initial purchase cost is realized more quickly
Servomotor
SPEED - Reaches 10,000 rpm • Brushless DC servomotors also operate at all speeds while maintaining rated load
EFFICIENCY - Designed to operate over wide range of voltages (as this is how their speed is varied) but efficiency drops with voltage
RELIABILITY - Physical motor issues minimal; demanding servo applications require careful sizing, or can threaten failure
POWER DENSITY - Capable of high peak torque for rapid acceleration
ACCURACY - Closed-loop servomotor operation utilizes feedback for speed accuracy to ±0.001% of base speed
COST - Price can be tenfold that of other systems
In the end, all industrial motor subtypes have strengths and weaknesses,plus application niches for which they’re most suitable. For example, many industrial applications are essentially constant torque, such as conveyors. Others, such as centrifugal blowers, require torque to vary as the square of the speed. In contrast, machine tools and center winders are constant horsepower, with torque decreasing as speed increases. Which motors are most suitable in these situations? As we will explore, the speed-torque relationship and efficiency requirements often determine the most appropriate motor.
This is the blog about industry automation, where is original research and aggregation of content about Industrial automation control system and other industry devices, motor, accessories, CNC solution, etc.
2016年12月13日星期二
2016年12月5日星期一
What is a Servo Control System
A servo control system is one of the most important and widely used forms of control system. Any machine or piece of equipment that has rotating parts will contain one or more servo control systems. The job of the control system may include:
* Maintaining the speed of a motor within certain limits, even when the load on the output of the motor might vary. This is called regulation.
* Varying the speed of a motor and load according to an externally set programme of values. This is called set point (or reference) tracking.

Servo motors are brushed or brushless servo motors with feedback, typically encoder or resolver. They can be rotary or linear motors. They require a complex closed loop control algorithm (such as the classic PID method). Normally the control loop has to be tuned, and servo dither can be a problem.. Due to the added control and feedback, typically servo systems are more expensive than stepper systems.
Servo motors typically have a peak torque of 3-10x the continuous torque, their torque curve is much flatter than the stepper curve, and the maximum speeds are much higher. Peak torque is a great thing; often, a system just needs extra power for a short time to accelerate, overcome friction, or such.
Our daily lives depend upon servo controllers. Anywhere that there is an electric motor there will be a servo control system to control it. Servo control is very important. The economy of the world depends upon servo control (there are other things to be sure – but stay with me on the control theme). Manufacturing industry would cease without servo systems because factory production lines could not be controlled, transportation would halt because electric traction units would fail, computers would cease because disk drives would not work properly and communications networks would fail because network servers use hard disk drives. Young people would become even more unbearable and they would complain more than they do now, because their music and games systems will not work without servo control.
Servo control systems are that important and it is vital to know about them. So pay attention and sit up straight – you are not on holiday and I am not writing this for the good of my health.
* Maintaining the speed of a motor within certain limits, even when the load on the output of the motor might vary. This is called regulation.
* Varying the speed of a motor and load according to an externally set programme of values. This is called set point (or reference) tracking.

Servo motors are brushed or brushless servo motors with feedback, typically encoder or resolver. They can be rotary or linear motors. They require a complex closed loop control algorithm (such as the classic PID method). Normally the control loop has to be tuned, and servo dither can be a problem.. Due to the added control and feedback, typically servo systems are more expensive than stepper systems.
Servo motors typically have a peak torque of 3-10x the continuous torque, their torque curve is much flatter than the stepper curve, and the maximum speeds are much higher. Peak torque is a great thing; often, a system just needs extra power for a short time to accelerate, overcome friction, or such.
Our daily lives depend upon servo controllers. Anywhere that there is an electric motor there will be a servo control system to control it. Servo control is very important. The economy of the world depends upon servo control (there are other things to be sure – but stay with me on the control theme). Manufacturing industry would cease without servo systems because factory production lines could not be controlled, transportation would halt because electric traction units would fail, computers would cease because disk drives would not work properly and communications networks would fail because network servers use hard disk drives. Young people would become even more unbearable and they would complain more than they do now, because their music and games systems will not work without servo control.
Servo control systems are that important and it is vital to know about them. So pay attention and sit up straight – you are not on holiday and I am not writing this for the good of my health.
2016年11月16日星期三
Hybrid Stepper Motor
The hybrid stepper motor uses the principles of the permanent magnet and variable reluctance stepper motors. In the hybrid motors, the rotor flux is produced by the permanet magnet and is directed by the rotor teeth to the appropriate parts of the airgap.
The main flux path is from the north pole of the magnet, into the end stack, across the airgrap through the stator pole, axially along the stator, through the stator pole, across the air gap and back to the magnet south pole via the other end stack.
There are usually 8 poles on the stator. Each pole has between 2 to 6 teeth. There is two phase winding. The coils on poles 1,3,5 and 7 are connected in series to form phase A while the coils on poles 2,4,6 and 8 are connected in series to form phase B. The windings A and B are energised alternately.
When phase A carries positive current, stator poles 1 and 5 become south and 3 and 7 become north. The rotor teeth with north and south polarity align with the teeth of stator poles 1 and 5 and 3 and 7 respectively. When phase A is de energised and phase Bis exicited, are energised alternately.
The torque in hybrid stepper motor is produced by the interaction of the rotor and the stator produced fluxes. The rotor field remains constant as it is produced by the permanent magnet. The motor torque T is proporatinal to the phase current.
Following are the main advantages of the hybrid stepper motor:
1. Very small step angles upto 1.8
2. Higher torque per unit volume which is more than in cae of variable reluctance motor
3. Due to permanet magnet, the motor has some detent torque which is absent in variable reluctance motor.
These are the various types of the stepper motors. After duscussing the various types and the operating principle, let us discuss the important parameters related to a stepper motor. The stepper motor characteristics are mainly the indication of its important parameters.
1. Holding Torque:
It is defined as the maximum static torque that can be qpplied to the shaft of an excited motor without causing a continuous rotaing.
2. Detent Torque:
It is defined as the maximum static torque that can be qpplied to the shaft of an unexcited motor without causing a continuous rotation.
Under this torque the rotor comes back to the normal rest position even if excitation ceases. Such positions of the rotor are referred as the detent positions.
3. Step Angle:
It is defined as the angular displacement of the rotor in response to each input pulse.
4. Critical Torque:
It is defined as the maximum load torque at which rotor does not move when an exciting winding is energised. This is also called pullout torque.
5. Limiting Torque:
It is defined for a given pulsing rate or stepping rate measured in pulses per second, as the maximum load torque at which motor follows the control pulses without missing any step. This is also called pull in torque.
6. Synchronous stepping rate:
It is defined as the maximum rate at which the motor can step wihout missing steps. The motor can start, stop or reverse at this rate.
7. Slewing rate:
It is deined as the maximum rate at which the motor can step unidirectionally. The slewing rate is much higher than the synchronous stepping rate. Motor will not be able to stop or reverse without missing steps at this rate.
The main flux path is from the north pole of the magnet, into the end stack, across the airgrap through the stator pole, axially along the stator, through the stator pole, across the air gap and back to the magnet south pole via the other end stack.
There are usually 8 poles on the stator. Each pole has between 2 to 6 teeth. There is two phase winding. The coils on poles 1,3,5 and 7 are connected in series to form phase A while the coils on poles 2,4,6 and 8 are connected in series to form phase B. The windings A and B are energised alternately.
When phase A carries positive current, stator poles 1 and 5 become south and 3 and 7 become north. The rotor teeth with north and south polarity align with the teeth of stator poles 1 and 5 and 3 and 7 respectively. When phase A is de energised and phase Bis exicited, are energised alternately.
The torque in hybrid stepper motor is produced by the interaction of the rotor and the stator produced fluxes. The rotor field remains constant as it is produced by the permanent magnet. The motor torque T is proporatinal to the phase current.
Following are the main advantages of the hybrid stepper motor:
1. Very small step angles upto 1.8
2. Higher torque per unit volume which is more than in cae of variable reluctance motor
3. Due to permanet magnet, the motor has some detent torque which is absent in variable reluctance motor.
These are the various types of the stepper motors. After duscussing the various types and the operating principle, let us discuss the important parameters related to a stepper motor. The stepper motor characteristics are mainly the indication of its important parameters.
1. Holding Torque:
It is defined as the maximum static torque that can be qpplied to the shaft of an excited motor without causing a continuous rotaing.
2. Detent Torque:
It is defined as the maximum static torque that can be qpplied to the shaft of an unexcited motor without causing a continuous rotation.
Under this torque the rotor comes back to the normal rest position even if excitation ceases. Such positions of the rotor are referred as the detent positions.
3. Step Angle:
It is defined as the angular displacement of the rotor in response to each input pulse.
4. Critical Torque:
It is defined as the maximum load torque at which rotor does not move when an exciting winding is energised. This is also called pullout torque.
5. Limiting Torque:
It is defined for a given pulsing rate or stepping rate measured in pulses per second, as the maximum load torque at which motor follows the control pulses without missing any step. This is also called pull in torque.
6. Synchronous stepping rate:
It is defined as the maximum rate at which the motor can step wihout missing steps. The motor can start, stop or reverse at this rate.
7. Slewing rate:
It is deined as the maximum rate at which the motor can step unidirectionally. The slewing rate is much higher than the synchronous stepping rate. Motor will not be able to stop or reverse without missing steps at this rate.
2016年11月14日星期一
The introduction of Planetary Gearbox
Planetary gears are very popular due to their advantages such as high power density, companctness, and multiple and large compact gear ratios and load sharing among planets. Gearing arrangement is comrised of four different elements that produce a wide range of speed ratios in compact layout. These elecments are, Sun gear, an extenally toothed ring gear co-axial with the gear train Annulus, an internally toothed ring gear coaxial with ghe gear train Planets, externally toothed gears with mesh with the sun and anulus, and Planet Carrier, a support structure for planets, co-axial with the train. Planetary gear system as shown in Figure 1 is typically used to perform speed reduction due to serveral advantages over conventional parallel shaft gear systems.
Planetary gears are also used to advantages over conventional parallel shaft gear systems. Planetary gears are also used to obtain high power density, large reduction in small volume, pure torsional reactions and multiple shafting. Another advantage of the planetary gearbox arrangement is load distribution. If the number of planets in the system are more the ability of load shearing is greater and the higher the torque density. The planetary gearbox arrangment also creats greater and the higher the torque density. The planetary gearbox arrangment also creates greater stability due to the even distribution of mass and increased rotational stiffiness.
In recent years, enhancement of interior quietness in passenger cars. Automobiles is an important factor for influencing occupant comfort. planetary gear box sets are essential components of automatic transmissions because of their compact size and wide gear ratio range. They produce high speed reductions in compact spaces, greater load sharing, higher torque to weight ratio, diminished bearing loads and reduced noise and vibration. A Despite their advantage, the noise induced by the vibration of planetary gear systems remains a key concern. Planetary gears have receive considerably less research attention than single mesh gear paris. This paper focus on the study o two PGTs with different phasing (angular positions) while keeping every individual set unchanged.
This figure shows that the basic layout planetary gear train in which there is one Sun gear. Three Planet gear and one ring gear. They can produce the high speed reduction in compact space and having greater load shearing capacity & high torque to weight ratio.
Planetary basics — ratios, helix angles, axial loads, crowning
A planetary gearhead takes a high-speed, low-torque input, say from an electric motor, then increases torque and reduces speed at the output by the gearhead ratio. This lets motors run at higher, more-efficient rpms in equipment that operates at low speeds. It also reduces inertia reflected back to the motor, increasing stability. And using a planetary gearhead often lets machine builders reduce the size and cost of motion-control hardware.
Planetary units with helical gears, rather than spur gears, have a larger contact ratio. The contact ratio is the number of teeth in mesh at any given moment. While typical spur gearing has a 1.5 contact ratio, helical gearing more than doubles it to 3.3. Benefits of higher contact ratios include:
• 30 to 50% more torque capacity than equivalent spur-type planetary gearing.
• Better load sharing, which increases life.
• Smoother and quieter operation.
• Backlash reduced by as much as 2 arc-min.
The gearhead’s helix angle also has a significant impact on performance because the greater the angle, the more teeth in the mesh at any one time. So increasing the helix angle from the typical 12° up to 15° raises torque capacity by 17 to 20%; and by as much as 40% over straight-cut spur gears. Gears with a 15° helix angle also emit less noise.
Planetary gears are also used to advantages over conventional parallel shaft gear systems. Planetary gears are also used to obtain high power density, large reduction in small volume, pure torsional reactions and multiple shafting. Another advantage of the planetary gearbox arrangement is load distribution. If the number of planets in the system are more the ability of load shearing is greater and the higher the torque density. The planetary gearbox arrangment also creats greater and the higher the torque density. The planetary gearbox arrangment also creates greater stability due to the even distribution of mass and increased rotational stiffiness.
In recent years, enhancement of interior quietness in passenger cars. Automobiles is an important factor for influencing occupant comfort. planetary gear box sets are essential components of automatic transmissions because of their compact size and wide gear ratio range. They produce high speed reductions in compact spaces, greater load sharing, higher torque to weight ratio, diminished bearing loads and reduced noise and vibration. A Despite their advantage, the noise induced by the vibration of planetary gear systems remains a key concern. Planetary gears have receive considerably less research attention than single mesh gear paris. This paper focus on the study o two PGTs with different phasing (angular positions) while keeping every individual set unchanged.
This figure shows that the basic layout planetary gear train in which there is one Sun gear. Three Planet gear and one ring gear. They can produce the high speed reduction in compact space and having greater load shearing capacity & high torque to weight ratio.
Planetary basics — ratios, helix angles, axial loads, crowning

Planetary units with helical gears, rather than spur gears, have a larger contact ratio. The contact ratio is the number of teeth in mesh at any given moment. While typical spur gearing has a 1.5 contact ratio, helical gearing more than doubles it to 3.3. Benefits of higher contact ratios include:
• 30 to 50% more torque capacity than equivalent spur-type planetary gearing.
• Better load sharing, which increases life.
• Smoother and quieter operation.
• Backlash reduced by as much as 2 arc-min.
The gearhead’s helix angle also has a significant impact on performance because the greater the angle, the more teeth in the mesh at any one time. So increasing the helix angle from the typical 12° up to 15° raises torque capacity by 17 to 20%; and by as much as 40% over straight-cut spur gears. Gears with a 15° helix angle also emit less noise.
2016年11月7日星期一
The Type of Gear Reducers
Helical gears are used in parallel shaft gear reducer motor. In helical gears, gear teeth are machined along a helical path with respect to the axis of rotation. Helical gears are commonly used with two-, three-, and in some cases even four-, five-, and six-stage speed reductions. In-line helical reducers are a variation of parallel shaft speed reducers configured such that the output and input shafts are in-line.
Spiral bevel gears are used when the input and output shafts of the gear reducers are required to be at right angles. The curve shape of the spiral bevel teeth makes gradual contacts, resulting in less noise during operation. Helical, parallel shaft, and helical bevel gear units have high operating efficiency, approximately 98% for each gear stage reduction.
Worm gears, are the most economical speed reducers, capable of providing a sizable speed reduction with a single gear set. The input and output shaft of these gears are at right angles to each other. However, becasue of the sliding contact between the worm pinion and the gear, the worm gear redcuer is less efficient. The efficiency decreases as the speed redcution ratio increases. For example, at a speed reduction ratio of 10:1, the efficiency of the worm gearbox may be approximately 90%. However, at a redution ratio of about 50:1, the efficiency of the worm reducer drops to about 70%. Gearbox manufactures offer worm gear reducer in helical bevel and helical worm design.
Helical, spiral bevel, and worm gears are external gears with the teeth on the outer periphery of the gears. In planetary gears the teeth profile is on the inside of a circular ring with meshing pinion. Planetary gears consist of an internal gear with a small pinion, known as a sun gear, surrounded by multiple planetary gears. These gears can provide high speed reduction ratios and are relatively compact in size. Gear reducer manufacturers also offer geared-motor, that consists of a factory assembled motor with the gear unit. Figure 12.34 shows a variety of gear reducer with motor configurations.
NMRV worm gear series also available as compact and flexibility. NMRV worm gear series also available as compact integral helical/worm option, has been designed with a view to modularity: low number of basic models can be applied to a wide range of power ratings guaranteeing top performance and reduction ratios from 5 to 1000.
2016年10月28日星期五
Stepper Drive Modes
This chapter has explained how to operate steppers by energizing one or two winding pairs at a tiem, but tere are a number of different ways to drive a stepper, and this discussion touches on four of them:
* Full-step (one phase on) mode - Each control signal energizes on winding.
* Full-step (two phases on) mode - Each control signal energizes two windings.
* Half-step mode - Each control signal alternates between energizing one and two windings.
* Microstep mode - The controller delivers sinusoidal signals to the stepper's windings.
Full-Step (One Phase On) Mode
The simplest way to control a stepper is to energize one winding at a time. This is the method discussed at the start of this chapter. Figure 4.15 shows what the signaling sequence looks lide when controlling a stepper in this mode.
With each control signal, the rotor truns to align itself with the energized winding. The rotor always turns through the stepper's rated step angle. That is, if a PM motor is rated for 7.5, each control signal causes it to turn 7.5.
Full-Step (Two Phase On) Mode
In the full-step (two phase on) mode, the controller energizes two windings at once. This turns the rotor through the stepper's rated angle, and the rotor always aligns itself between two windings. Figure 4.16 illustrates one rotation of a stepper motor driven in this mode.
Figure 4.17 shows what the corresponding drive sequence looks like.
The main advantage of this mode over full-step (one phase on) is that it improves the motor's torque. Because two windings are always on, torque increases by approximately 30%-40%. The disadvantage is that the power supply has to provide twice as much current to turn the stepper.
Half-Step Mode
The half-step mode is like a combination of the two full-step modes. That is, the controller alternates between energizing one winding and two windings. Figure 4.18 depicts three rotations of a stepper in half-step mode.
Figure 4.19 illustrates a control signal for a stepper motor driven in half-step mode.
In this mode, the rotor aligns itself with windings (when one winding is energized) and between windings (when two windings are energized). This effectively reduces the motor's step angle by half. That is, if the stepper's step angle is 1.8, it will trun at 0.9 in half-step mode.
The disadvantage of this mode is that, when a single winding is energized, the rotor turns with approximately 20% less toruqe. This can be compenstated for by increasing the current.
Microstep Mode
The purpose of microstep mode is to have the stepper turn as smoothly as possible. This requires dividing the energizing pulse into potentially hundreds of control signals. Common numbers of division are 8,64,and 256. If the energizing pulse is divided into 256 signals, a 1.8 stepper will turn at 1.8/256=0.007 per control signal.
In this mode, the controller delivers current in a sinusoidal pattern. Successive windings receive a delayed version of this sinusoid. Figure 4.20 gives an idea of what this looks like.
Using this mode reduces torque by nearly 30%, but another disadvantage involes speed. As the width of a control signal decrease, the ability of the motor to respond also decrease. Therefore, if the controller delivers rapid pulses to the stepper in microstep mode, the motor may not turn in a reliable fashion.
* Full-step (one phase on) mode - Each control signal energizes on winding.
* Full-step (two phases on) mode - Each control signal energizes two windings.
* Half-step mode - Each control signal alternates between energizing one and two windings.
* Microstep mode - The controller delivers sinusoidal signals to the stepper's windings.
Full-Step (One Phase On) Mode
The simplest way to control a stepper is to energize one winding at a time. This is the method discussed at the start of this chapter. Figure 4.15 shows what the signaling sequence looks lide when controlling a stepper in this mode.
With each control signal, the rotor truns to align itself with the energized winding. The rotor always turns through the stepper's rated step angle. That is, if a PM motor is rated for 7.5, each control signal causes it to turn 7.5.
Full-Step (Two Phase On) Mode
In the full-step (two phase on) mode, the controller energizes two windings at once. This turns the rotor through the stepper's rated angle, and the rotor always aligns itself between two windings. Figure 4.16 illustrates one rotation of a stepper motor driven in this mode.
Figure 4.17 shows what the corresponding drive sequence looks like.
The main advantage of this mode over full-step (one phase on) is that it improves the motor's torque. Because two windings are always on, torque increases by approximately 30%-40%. The disadvantage is that the power supply has to provide twice as much current to turn the stepper.
Half-Step Mode
The half-step mode is like a combination of the two full-step modes. That is, the controller alternates between energizing one winding and two windings. Figure 4.18 depicts three rotations of a stepper in half-step mode.
Figure 4.19 illustrates a control signal for a stepper motor driven in half-step mode.
In this mode, the rotor aligns itself with windings (when one winding is energized) and between windings (when two windings are energized). This effectively reduces the motor's step angle by half. That is, if the stepper's step angle is 1.8, it will trun at 0.9 in half-step mode.
The disadvantage of this mode is that, when a single winding is energized, the rotor turns with approximately 20% less toruqe. This can be compenstated for by increasing the current.
Microstep Mode
The purpose of microstep mode is to have the stepper turn as smoothly as possible. This requires dividing the energizing pulse into potentially hundreds of control signals. Common numbers of division are 8,64,and 256. If the energizing pulse is divided into 256 signals, a 1.8 stepper will turn at 1.8/256=0.007 per control signal.
In this mode, the controller delivers current in a sinusoidal pattern. Successive windings receive a delayed version of this sinusoid. Figure 4.20 gives an idea of what this looks like.
Using this mode reduces torque by nearly 30%, but another disadvantage involes speed. As the width of a control signal decrease, the ability of the motor to respond also decrease. Therefore, if the controller delivers rapid pulses to the stepper in microstep mode, the motor may not turn in a reliable fashion.
2016年10月25日星期二
Sychronous type AC Servo Motor
The stator consists of a cylindrical frame and a stator core. The stator core is located in the frame and an armature coil is wound around the stator core. The end of the coil is connected with a lead wire and current is provide from the lead wire. The rotor consists of a shaft and a permanent magnet and the permanent magnet is attached to the outside of the shaft. In a synchronous type AC servo motor, the magnet is attached to a rotor and an armature coil is wound around the stator unlike the DC servo motor. Therefore, the supply of current is possible from the outside without a stator and a synchronous type AC servo motor is called a "brushless servo motor" because of this structural characteristic. Because this structure makes it possible to cool down a stator core directly from the outside, it is possible to resist an increase in temeprature. Also, because a synchronous type AC servo motor does not have the limitation of maximum velocity due to recification spark, a good characteristic of torque in the high-speed range can be obtained. In additon, because this type of motor has no brush, it can be operated for a long time without maintenace.
Like a DC servo motor, this type of AC servo motor uses an optical encoder or a resolver as a detector of rotation velocity. Also, a ferrite magnet or a rate earth magnet is used for the magnet which is built into the rotor and plays the role of a field system.
In this type of AC Servo Motor, because an armature contribution is linearly proportional to torque. Stop is easy and dynamic brake wordks during emergency stop. However, because a permanent magnet is use, the structure is very complex and the detection of position of the rotor is needed. The current from the armature includes high frequency current and the high frequecy current is the source of toruqe ripple and vibration.
Like a DC servo motor, this type of AC servo motor uses an optical encoder or a resolver as a detector of rotation velocity. Also, a ferrite magnet or a rate earth magnet is used for the magnet which is built into the rotor and plays the role of a field system.
In this type of AC Servo Motor, because an armature contribution is linearly proportional to torque. Stop is easy and dynamic brake wordks during emergency stop. However, because a permanent magnet is use, the structure is very complex and the detection of position of the rotor is needed. The current from the armature includes high frequency current and the high frequecy current is the source of toruqe ripple and vibration.
2016年10月18日星期二
The need for variable speed drives
There are many and diverse reasons for using variable speed drives. Some applictaions, such as paper making machines, cannot run without them while others, such as centrifugal pumps, can benefit from energy savings.
In general, variable speed drives are used to:
Match the speed of a drive to the process requirements
Match the torque of a drive to the process requirements
Save energy and improve efficency
The needs for speed and torque control are usually fairly obvious. Modern electrical VSDs can be used to accurately maintain the speed of a driven machine to within ±0.1%, independent of load, compared to the speed regulation possible with a conventional fixed speed squirrel cage induction motor, where the speed can vary by as much as 3% from no load to full load.
The benefits of energy savings are not always fully appreciated by many users. These savings are particulary apparent with centrifugal pumps and fans, where load torque increas as the square of the speed and power consumption as the cube of the speed. Substantial cost savings can be achieved in some applications.
An everyday example, which illustrates the benefits of variable speed control, is the motorcar. It has become such as an integral part of our lives that we seldom think about the technology that it represents or that it is simply a variable speed platfrom. It is used here to illustrate how variable speed drives are used to improve the speed, torque and energy performance of a machine.
It is intuitively obvious that the speed of a motorcar must continuously be controlled by the driver (the operator) to match the traffic conditions on the road (the process). In a city, it is necessary to obey speed limits, avoid collisions and to start, accelerate, decelerate and stop when required. On the open road, the main objective is to get to a destination safely in the shortest time without exceeding the speed limit. The two main controls that are used to control the speed are the accelerator, which controls the driving torque, and the brake, which adjusts the load torque. A motorcar could not be safely operated in city traffic or on the open road without these two controls. The driver must continuously adjust the fuel input to the engine (the drive) to maintain a consistant speed in spite of the changes in the load, such as an uphill, downhill or strong wind conditions. On other occasions he may have to use the brake to adjust the load and slow the vehicle down to standstill.
Another important issue for most drivers is the cost of fuel or the cost of energy consumption. The speed is controlled via the accelerator that controls the fuel input to the engine. By adjusting the accelerator position, the energy consumption is kept to a minimum and is mached to the speed and load conditions. Imageine the high fuel comsumption of a vehicle using a fixed accelerator setting and controlling the speed by means of the brake position.
In general, variable speed drives are used to:
Match the speed of a drive to the process requirements
Match the torque of a drive to the process requirements
Save energy and improve efficency
The needs for speed and torque control are usually fairly obvious. Modern electrical VSDs can be used to accurately maintain the speed of a driven machine to within ±0.1%, independent of load, compared to the speed regulation possible with a conventional fixed speed squirrel cage induction motor, where the speed can vary by as much as 3% from no load to full load.
The benefits of energy savings are not always fully appreciated by many users. These savings are particulary apparent with centrifugal pumps and fans, where load torque increas as the square of the speed and power consumption as the cube of the speed. Substantial cost savings can be achieved in some applications.
An everyday example, which illustrates the benefits of variable speed control, is the motorcar. It has become such as an integral part of our lives that we seldom think about the technology that it represents or that it is simply a variable speed platfrom. It is used here to illustrate how variable speed drives are used to improve the speed, torque and energy performance of a machine.
It is intuitively obvious that the speed of a motorcar must continuously be controlled by the driver (the operator) to match the traffic conditions on the road (the process). In a city, it is necessary to obey speed limits, avoid collisions and to start, accelerate, decelerate and stop when required. On the open road, the main objective is to get to a destination safely in the shortest time without exceeding the speed limit. The two main controls that are used to control the speed are the accelerator, which controls the driving torque, and the brake, which adjusts the load torque. A motorcar could not be safely operated in city traffic or on the open road without these two controls. The driver must continuously adjust the fuel input to the engine (the drive) to maintain a consistant speed in spite of the changes in the load, such as an uphill, downhill or strong wind conditions. On other occasions he may have to use the brake to adjust the load and slow the vehicle down to standstill.
Another important issue for most drivers is the cost of fuel or the cost of energy consumption. The speed is controlled via the accelerator that controls the fuel input to the engine. By adjusting the accelerator position, the energy consumption is kept to a minimum and is mached to the speed and load conditions. Imageine the high fuel comsumption of a vehicle using a fixed accelerator setting and controlling the speed by means of the brake position.
2016年9月22日星期四
Gear Motors
A gear motor develops an output torque at its shaft by allowing hydraulic pressure to act on gear teeth. A gear motor consists basically of a housing with inlet and outlet ports, and a rotating group made up of two gears. One gear is attached to a shaft that is connected to a load. The other gear is the driven gear. The various commonly used gear motors are shown in Fig.2.16.
In a gear motor, the imbalance necessary for motor operation is caused by gear teeth unmeshing. The inlet is subjected to system pressure and the outlet is at return line pressure. As the gear teeth unmesh, all teeth subjected to system pressure are hydraulically balanced except for one side of one tooth on one gear tooth. The larger the gear tooth or the higher the pressure,the more torque is produced.
An internal gear motor consists of one external gear which meshes whith the teeth on the inside circumference of a larger gear. A popular type of internal gear motor in industrial systems is the gerotor motor. This motor is an internal gear motor with an inner drive gear and an outer driven gear which has one more tooth than the inner gear. The inner gear is attached to a shaft which is connected to a load. The imbalance in a gerotor motor is cuased by the difference in gear area exposed to hydraulic pressure at the motor inlet.
Fluid pressure acting on these unequally exposed teeth results in a torque at the motor shaft. The larger the gear or the higher the pressure, the more torque will be developed at the shaft. Fluid entering the rotating group of a gerotor motor is separated from the fluide exiting the motor by means of a port plate with kindey-shaped inlet and outlet ports.
When selecting a gear motor, an important consideration is the degree of gear service and gear life based on the load conditions to which the motor will be subjected. Gear motors are divided into three classes. Each class uses different gear sizes to handle specific load conditions. Each class gives about the same life for the gears. The American Gear Manufacturer's Association has defined three operating conditions commonly found in industrial service and has established three standard gear classifications to meet these conditions:
Class I For steady loads within the motor rating of 8 hours per day duration, or for intermittent operation under moderate stock conditions.
Class II For 24-hour operation at steady loads within the motor rating, or 8-hour operation under moderate shock conditions.
Class III For 24-hour operation under moderate shock condition, or 8-hour operation under heavy shock conditions.
For conditions that are more severe than those covered by Class III gears, a fluid drive unit may be incorporated in assembly to cushion the shock to an acceptable value.
To achieve multiple speeds, separte units are available with a transmission comparable to that of an automobile. These units must be assembled with the motor and the driven machine. Because the amout of power lost in gearing is very small, the multiple drive has essentially constant horsepower. In other words, as the output speed is decreased, the torque is increased. Generally, this means that larger shaft sizes are needed for the output side.
In a gear motor, the imbalance necessary for motor operation is caused by gear teeth unmeshing. The inlet is subjected to system pressure and the outlet is at return line pressure. As the gear teeth unmesh, all teeth subjected to system pressure are hydraulically balanced except for one side of one tooth on one gear tooth. The larger the gear tooth or the higher the pressure,the more torque is produced.
An internal gear motor consists of one external gear which meshes whith the teeth on the inside circumference of a larger gear. A popular type of internal gear motor in industrial systems is the gerotor motor. This motor is an internal gear motor with an inner drive gear and an outer driven gear which has one more tooth than the inner gear. The inner gear is attached to a shaft which is connected to a load. The imbalance in a gerotor motor is cuased by the difference in gear area exposed to hydraulic pressure at the motor inlet.
Fluid pressure acting on these unequally exposed teeth results in a torque at the motor shaft. The larger the gear or the higher the pressure, the more torque will be developed at the shaft. Fluid entering the rotating group of a gerotor motor is separated from the fluide exiting the motor by means of a port plate with kindey-shaped inlet and outlet ports.
When selecting a gear motor, an important consideration is the degree of gear service and gear life based on the load conditions to which the motor will be subjected. Gear motors are divided into three classes. Each class uses different gear sizes to handle specific load conditions. Each class gives about the same life for the gears. The American Gear Manufacturer's Association has defined three operating conditions commonly found in industrial service and has established three standard gear classifications to meet these conditions:
Class I For steady loads within the motor rating of 8 hours per day duration, or for intermittent operation under moderate stock conditions.
Class II For 24-hour operation at steady loads within the motor rating, or 8-hour operation under moderate shock conditions.
Class III For 24-hour operation under moderate shock condition, or 8-hour operation under heavy shock conditions.
For conditions that are more severe than those covered by Class III gears, a fluid drive unit may be incorporated in assembly to cushion the shock to an acceptable value.
To achieve multiple speeds, separte units are available with a transmission comparable to that of an automobile. These units must be assembled with the motor and the driven machine. Because the amout of power lost in gearing is very small, the multiple drive has essentially constant horsepower. In other words, as the output speed is decreased, the torque is increased. Generally, this means that larger shaft sizes are needed for the output side.
2016年9月20日星期二
Inserting Parametric PLC Modules
A programmable logic controller (PLC) or programmable controller is a digital computer that is used to automatically regulate the industrial process. For example, comtrolling machinery on assembly lines of factor. This controller is designed to meet a range of industrial activities such as multiple inputs and output arrangements, extended temperature ranges, giving immunity to electrical noise, and providing resistance to vibration. The programs, designed to regulate the machine operation, are usually stored in a battery-backed or non-volatile memory. A PLC is an instance of a real time system becuase output results are needed to be produced in response to input conditions within a time-bound period; else, it will result in an unintended operation. Over the years, the functionality of PLC has evolvoed to accommodate sequential relay control, motion control, process control, distributed control systems, and networking. In PLC, microprocessor controlled interface is inbuilt and is designed to control or monitor some other I/O functions. Being an industrial computer control system, it always monitors the state of input devices and makes decisions on the basis of custom program for controlling the state of devices connected as outputs.
Inserting Parametric PLC Modules
AutoCAD Electrical can generate PLC I/O modules in different graphical styles through parametric generation technique on demand. These modules are generate by a database file and a library of symbol blocks. PLC I/O modules can be inserted as independent symbols. PLC modules behave like other schematic components. These modules are AutoCAD blocks containing attributes for connection points, tagging and so on.
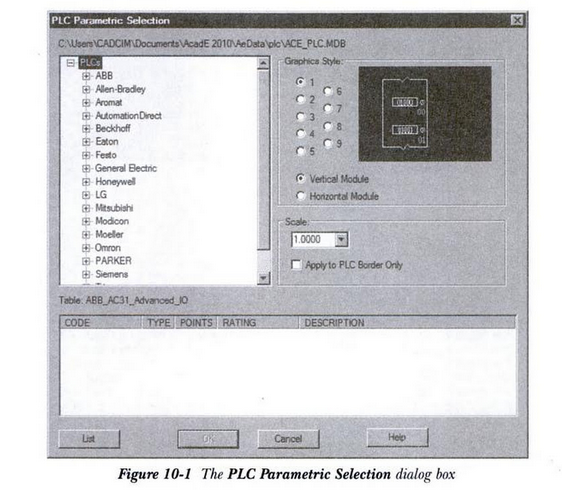
The Insert PLC (Parametric) tool is used to insert a PLC module parametrically. To do so, choose the Insert PLC (PLarametric) button from the Insert Components panel of the Schematic tab; the PLC Parametric Selection dialog box will be displayed, as shown in Figure 10-1. Using this dialog box, you can select the PLC module and its graphics that you want to insert in a drawing. The different options and areas in this dialog box are discussed next.
Manufacture Catalog Tree
The Manufacture Catalog tree, shown in Figure 10-2, displays a list of PLC modules. This list can be filtered by selecting the manufacturer, series, and type of PLC. The data displayed in the Manufacturer Catalog tree is stored in the ace_plc.mdb database file.
You can selet a PLC module from the Manufacturer Catalog tree. To do so, click on the + sign on the requried manfacturers module; PLC modules of the selected manafacturer will be displayed. Select the requried module from the module list; the detailed information of the selected module will be displayed at the lower part of the PLC Parametric Selection dialog box, as shown in Figure 10-3.
After specifying the required values in the I/O Point dialog box, choose the OK button from this dialog box; the I/O Address dialog box will be displayed, as shown in Figure 10-6. Using this dialog box, you can specify the address for the first I/O point.
The values in the Quick picks drop-down list are based on the values that you have specified in the I/O Point dialog box in the Rack and SLOT edit boxes. Select the required value from the Quick picks drop-down list; the value will be displayed in the Beginning address edit box. Alternatively, enter a required value for the first I/0 address of a PLC module in the Beginning address edit box. Note that the other I/O points of a module will be incremented based on the value specified in the Beginning address edit box.
Choose the List button in the I/O Address dialog box; the Report Generator dialog box will be displayed. This dialog box display the information of the selected PLC module.
After specifying the required options in the I/O Address dialog box, choose the OK button in this dialog box; the selected PLC module will be inserted into the drawing.
Inserting Parametric PLC Modules
AutoCAD Electrical can generate PLC I/O modules in different graphical styles through parametric generation technique on demand. These modules are generate by a database file and a library of symbol blocks. PLC I/O modules can be inserted as independent symbols. PLC modules behave like other schematic components. These modules are AutoCAD blocks containing attributes for connection points, tagging and so on.
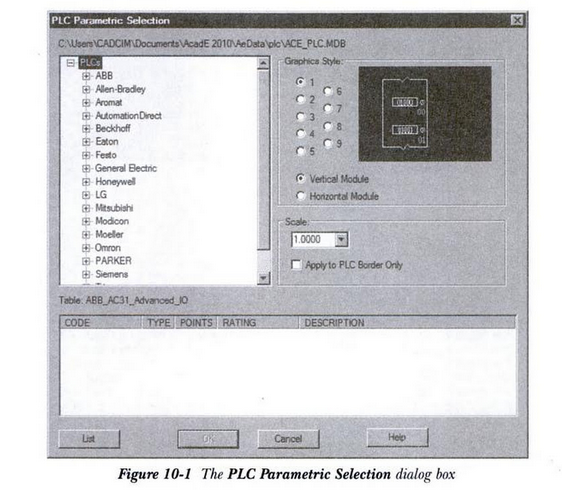
The Insert PLC (Parametric) tool is used to insert a PLC module parametrically. To do so, choose the Insert PLC (PLarametric) button from the Insert Components panel of the Schematic tab; the PLC Parametric Selection dialog box will be displayed, as shown in Figure 10-1. Using this dialog box, you can select the PLC module and its graphics that you want to insert in a drawing. The different options and areas in this dialog box are discussed next.
Manufacture Catalog Tree
The Manufacture Catalog tree, shown in Figure 10-2, displays a list of PLC modules. This list can be filtered by selecting the manufacturer, series, and type of PLC. The data displayed in the Manufacturer Catalog tree is stored in the ace_plc.mdb database file.
You can selet a PLC module from the Manufacturer Catalog tree. To do so, click on the + sign on the requried manfacturers module; PLC modules of the selected manafacturer will be displayed. Select the requried module from the module list; the detailed information of the selected module will be displayed at the lower part of the PLC Parametric Selection dialog box, as shown in Figure 10-3.
After specifying the required values in the I/O Point dialog box, choose the OK button from this dialog box; the I/O Address dialog box will be displayed, as shown in Figure 10-6. Using this dialog box, you can specify the address for the first I/O point.
The values in the Quick picks drop-down list are based on the values that you have specified in the I/O Point dialog box in the Rack and SLOT edit boxes. Select the required value from the Quick picks drop-down list; the value will be displayed in the Beginning address edit box. Alternatively, enter a required value for the first I/0 address of a PLC module in the Beginning address edit box. Note that the other I/O points of a module will be incremented based on the value specified in the Beginning address edit box.
Choose the List button in the I/O Address dialog box; the Report Generator dialog box will be displayed. This dialog box display the information of the selected PLC module.
After specifying the required options in the I/O Address dialog box, choose the OK button in this dialog box; the selected PLC module will be inserted into the drawing.
2016年9月13日星期二
DSP-BASED Control of Stepper Motors
A stepper motor is an electric machine that rotates in discrete angular increments or steps. Stepper motors are operated by applying current pulses of a specific frequency to the inputs of the motor. Each pulse applied to the motor causes its shaft to the motor causes its shaft to move a certain angle of rotation, called a stepping angle. Since the input signal is converted directly into a requested shaft position without any rotor position sensors or feedback, the stepper motor has the following advantages:
The stepper motor has salient poles on both the stator and the rotor, andnormally only the stator poles hold the poly-phase windings called the controlwindings. Usually stepper motors are classified as:
While each of these types of stepper motors has merit, hybrid stepper motorsare becoming more popular in industrial applications. In this chapter, we focus onthe principles and implementation of a hybrid stepper motor control system usingthe LF2407 DSP controller.
The operation of the stepper motor relies on the simple principle of magneticattraction. This principle states that opposite magnetic poles attract while like polesrepel each other. If the windings are excited in the correct sequence, the rotor will rotate following a certain direction. The basic operation of a stepper motor can beclassified generally as either full step mode or half step mode. These modes are discussed in detail in the following section using the simplified stepper motorconstruction shown in Fig. 8.1.
Full-step Mode
If none of the stator windings are excited, an attraction between the stator polesand rotor teeth still exists because the PM rotor is trying to minimize the reluctanceof the magnetic flux path from one end to the other. As a result, the rotor will tend to rest at one of the rest equilibrium positions. From Fig. 8.1, a rest position existswhen a pair of rotor teeth are aligned with two of the stator poles. In the case ofFig. 8.1, the rotor is aligned with pole 1 and pole 3 on the stator. There are a total of12 possible equilibrium positions for a 4-phase, 6-pole stepper motor. The force ortorque that holds the rotor in one of these positions is called the detent torque. The value of the detent torque is usually small because no current flows through thestator windings.
Half-Step Mode
The stepper motor operation discussed rotates 300 per step. In the half step mode, alternately exciting one winding, then exciting two windings, will cause therotor to move through only 15 degree per step. Though there is a slight loss of thetorque while the single winding is being excited, half-step operation allows forsmoother operation at lower speeds and less overshoot at the end of each step. The excitation sequence of the stator windings in half-step mode is given in Table 8.3.During this operation, each switch between the two nearest modes will cause a 450 shift of stator field which results in a 150 rotation of the rotor. A total of 24steps are required for a complete revolution, double of what is required for full stepmodes.
Micro Step Mode
For the operating modes discussed previously, the same amount of current flows through the energized stator windings. However, if the currents are not equal, the rotor will be shifted towards the stator pole with the higher current. The amount of deviation is proportionate to the values of the currents in each winding. This principle is utilized in the microstep mode. During this mode, each basic full mode step can be divided into as many as 500 microsteps, providing the proper current profile is applied.
- Rotational speed proportional to the frequency of input pulses
- Digital control of speed and position
- No need of feedback sensor for open loop control Excellent acceleration and deceleration responses to step commands
![]() |
Leadshine 57HS09 Stepper Motor |
The stepper motor has salient poles on both the stator and the rotor, andnormally only the stator poles hold the poly-phase windings called the controlwindings. Usually stepper motors are classified as:
- Active rotor (permanent magnet rotor)
- Reactive rotor (reluctance type)
- Hybrid motors (combining the operating principles of the permanentmagnet (PM) and reluctance stepper motor)
While each of these types of stepper motors has merit, hybrid stepper motorsare becoming more popular in industrial applications. In this chapter, we focus onthe principles and implementation of a hybrid stepper motor control system usingthe LF2407 DSP controller.
The operation of the stepper motor relies on the simple principle of magneticattraction. This principle states that opposite magnetic poles attract while like polesrepel each other. If the windings are excited in the correct sequence, the rotor will rotate following a certain direction. The basic operation of a stepper motor can beclassified generally as either full step mode or half step mode. These modes are discussed in detail in the following section using the simplified stepper motorconstruction shown in Fig. 8.1.
Full-step Mode
If none of the stator windings are excited, an attraction between the stator polesand rotor teeth still exists because the PM rotor is trying to minimize the reluctanceof the magnetic flux path from one end to the other. As a result, the rotor will tend to rest at one of the rest equilibrium positions. From Fig. 8.1, a rest position existswhen a pair of rotor teeth are aligned with two of the stator poles. In the case ofFig. 8.1, the rotor is aligned with pole 1 and pole 3 on the stator. There are a total of12 possible equilibrium positions for a 4-phase, 6-pole stepper motor. The force ortorque that holds the rotor in one of these positions is called the detent torque. The value of the detent torque is usually small because no current flows through thestator windings.
Half-Step Mode
The stepper motor operation discussed rotates 300 per step. In the half step mode, alternately exciting one winding, then exciting two windings, will cause therotor to move through only 15 degree per step. Though there is a slight loss of thetorque while the single winding is being excited, half-step operation allows forsmoother operation at lower speeds and less overshoot at the end of each step. The excitation sequence of the stator windings in half-step mode is given in Table 8.3.During this operation, each switch between the two nearest modes will cause a 450 shift of stator field which results in a 150 rotation of the rotor. A total of 24steps are required for a complete revolution, double of what is required for full stepmodes.
Micro Step Mode
For the operating modes discussed previously, the same amount of current flows through the energized stator windings. However, if the currents are not equal, the rotor will be shifted towards the stator pole with the higher current. The amount of deviation is proportionate to the values of the currents in each winding. This principle is utilized in the microstep mode. During this mode, each basic full mode step can be divided into as many as 500 microsteps, providing the proper current profile is applied.
2016年9月8日星期四
Spindle Motors
The motor that spins the platters is called the spindle motor because it is connected to the spindle around which the platters revolve. Spindle motors in hard disk drives are always connected directly; no belts or gears are involoved. The motor must be free of noise and vibration; otherwise, it can transmit a rumble to the platters, which can disrupt reading and writing operations.
The spindle motor also must be precisely controlled for speed. The platters in hard disk drives revolve at speeds ranging from 3600rpm to 15000rpm (60-250 revolutions per second) or more, and the motor has a control circuit with a feedback loop to monitor and control this speed precisely. Because the speed control must be automatic, hard drives do not have a motor-speed adjustment. Some diagostics programs claim to measure hard drive rotation speed, but all these programs do is estimate the rotational speed by the timing at which sectors pass under the heads.
There is actually no way for a program to meause the hard disk drive's rotational speed; this measurement can be made only with sophisticated test equipment. Don't be alarmed if some diagnostics program tells that your drive is spinning at an incorrect speed; most likely, the program is wrong, not the drive. Platter rotation and timeing information is not provided through the hard disk controller interface. In the past, software could give approximated rotational speed estimates by performing multiple sector read requests and timing them, but this was vaild only when all drives had the same number of sectors per track and spun at the same speed. Zoned-bit recording combined with the many various rotational speeds used by modern drives, not to mention built-in buffers and caches-means that these calcualtion estimates can't be performed accurately by software.
On most drives, the spindle motor is on the bottom of the drive, just below the sealed HDA. Many drives today, however have the spindle motor built directly into the platter hub inside the HDA. By using an intermal hub spindle motor, the manufacture can stack more platter in the drive because the spindle motor takes up no vertical space.
Traditionally, spindle motors have used ball bearings in their design, but limitations in their performance have now caused drive manufactures to look for alternatives. The main problem with ball bearings is that they have approximately 0.1 micro inch (millionths of an inch) of runout, which is lateral of modern drives, it has become a problem. This runout allows the platters to move randomly that displus the metal-to-metal contact nature of ball bearings allows an excessive amount of mechanical noise and vibration to be generated, and that is becoming a problem for drives that spin at higher speeds.
The solution is a new type of bearing called a fluld dynamic bearing, which uses a highly viscous lubrication flud between the spindle and sleeve in the motor. Thi flud serves to dampen vibrations and movement, allowing runout to be reduced to 0.01 micro inches or less. Fluid dynamic bearings also allow for better shock resistance, improved speed control, and reduced noise generation. Several of the more advanced drives on the market today already incorporated fluid dynamic bearings, especially those designed for very high spindle speeds, high areal densities, or low noise. Over the next few years, I expect to see fluid dynamic bearings become standard issue in most hard drives.
The spindle motor also must be precisely controlled for speed. The platters in hard disk drives revolve at speeds ranging from 3600rpm to 15000rpm (60-250 revolutions per second) or more, and the motor has a control circuit with a feedback loop to monitor and control this speed precisely. Because the speed control must be automatic, hard drives do not have a motor-speed adjustment. Some diagostics programs claim to measure hard drive rotation speed, but all these programs do is estimate the rotational speed by the timing at which sectors pass under the heads.
There is actually no way for a program to meause the hard disk drive's rotational speed; this measurement can be made only with sophisticated test equipment. Don't be alarmed if some diagnostics program tells that your drive is spinning at an incorrect speed; most likely, the program is wrong, not the drive. Platter rotation and timeing information is not provided through the hard disk controller interface. In the past, software could give approximated rotational speed estimates by performing multiple sector read requests and timing them, but this was vaild only when all drives had the same number of sectors per track and spun at the same speed. Zoned-bit recording combined with the many various rotational speeds used by modern drives, not to mention built-in buffers and caches-means that these calcualtion estimates can't be performed accurately by software.
On most drives, the spindle motor is on the bottom of the drive, just below the sealed HDA. Many drives today, however have the spindle motor built directly into the platter hub inside the HDA. By using an intermal hub spindle motor, the manufacture can stack more platter in the drive because the spindle motor takes up no vertical space.
Traditionally, spindle motors have used ball bearings in their design, but limitations in their performance have now caused drive manufactures to look for alternatives. The main problem with ball bearings is that they have approximately 0.1 micro inch (millionths of an inch) of runout, which is lateral of modern drives, it has become a problem. This runout allows the platters to move randomly that displus the metal-to-metal contact nature of ball bearings allows an excessive amount of mechanical noise and vibration to be generated, and that is becoming a problem for drives that spin at higher speeds.
The solution is a new type of bearing called a fluld dynamic bearing, which uses a highly viscous lubrication flud between the spindle and sleeve in the motor. Thi flud serves to dampen vibrations and movement, allowing runout to be reduced to 0.01 micro inches or less. Fluid dynamic bearings also allow for better shock resistance, improved speed control, and reduced noise generation. Several of the more advanced drives on the market today already incorporated fluid dynamic bearings, especially those designed for very high spindle speeds, high areal densities, or low noise. Over the next few years, I expect to see fluid dynamic bearings become standard issue in most hard drives.
2016年9月6日星期二
Mechanical Overview of Servo Motors
Servo motors have serval distinct characteristics that sperate them from their stepper counterparts. The biggest is the lack of direct gearing between the rotor and the output shaft. This eliminates the backlash and cogging behaviors found ins steppers, where there is period of slop between the gear teeth before movement actually begins, and where the shaft continues to move after the motor has stopped. This can lead to jerky starts and stops, as well as a time delay in movement. This does not impede static positioning performance markedly, but it presents major issues when on-the-fly velocity changes or hard starts/stops are needed.
A model of a typical radial brushless DC servo motor is shown before in figure 1.1 For a long time, servo motors used brushes to transfer current from the static winding to the rotor, but this would lead to wear on the brushes, in turn shortening the lifespan of the motor. With the advent of electronic motor controllers, the brusheless design was adopted, which uses control electronics to vary the currents phases to the motor's windings in the same way the brushes do. For the rest of this paper, all mention of servo motors will be of the brusheless type.
Looking at figure 1.1 below, there are several objects of interest. First are the armature windings (held by the stator), which create a magnetic field that travels through the air gap to the permanent magnets on the rotor. Even though there are normally no gears in a servo motor, cogging can still exist, as there are gaps between the magnets on the rotor where the flux decrease, though this only becomes noticeable at low speeds. This type of congging in servos is perhaps more accurately termed "detent torque." There are two ways to minimize this type of cogging, the most common being the addition of some gearing to the drive shaft. This allow the motor to run at a higher speed out of its cogging region, but does not compromise power output or precision, thought it can induce some backlash. The other way of minimizing cogging is to skew the magnets on the rotor so that a radial line from the center of the rotor always intersects a magnet at least once. When using a motor without gearing, it is known as a direct drive motor. This allows for the best transfer of power to the load, and avoids any of the negative aspects of gearing previously mentioned. A feature in newer servo motors (including the Bodine models used in this thesis) is the use of an ironless stator, which eliminates iron saturation, a situation where the magnetic properities of the iron limit how much current can be applied to the windings. Inducing iron saturation too ofen will cause overheating and possibly damage the winding or magnets. With an ironless stator, rotor magnet skewing is not necessary, as the magnetic fields aren't influenced by the material of the stator. Also, since the only mechanical connection between the shaft and the body is through the bearings, friction is very low (especialy when using ball bearings).
In high torque motors such as the ones used in this thesis, the rotor actually consists of two plates of permanet magnets sandwiching the stator, which allows for a major increase in torque. This feature only exists in axial flux motors, due to the design where the stator lies in between the rotors, whereas in radial flux servos, the rotor is completely enclosed by the stator. The majority of the heat dissipated from a servo motor comes from the stator, so its outside location adis in cooling. In fact, the main limiting fator in the power of a servo motor is the heat capacity of the stator and the armature windings.
Fasttobuy Servo Motor On Sale In this September
If you are interested in these servo motor, you can click this link: https://www.fasttobuy.com/specials.html
A model of a typical radial brushless DC servo motor is shown before in figure 1.1 For a long time, servo motors used brushes to transfer current from the static winding to the rotor, but this would lead to wear on the brushes, in turn shortening the lifespan of the motor. With the advent of electronic motor controllers, the brusheless design was adopted, which uses control electronics to vary the currents phases to the motor's windings in the same way the brushes do. For the rest of this paper, all mention of servo motors will be of the brusheless type.
Looking at figure 1.1 below, there are several objects of interest. First are the armature windings (held by the stator), which create a magnetic field that travels through the air gap to the permanent magnets on the rotor. Even though there are normally no gears in a servo motor, cogging can still exist, as there are gaps between the magnets on the rotor where the flux decrease, though this only becomes noticeable at low speeds. This type of congging in servos is perhaps more accurately termed "detent torque." There are two ways to minimize this type of cogging, the most common being the addition of some gearing to the drive shaft. This allow the motor to run at a higher speed out of its cogging region, but does not compromise power output or precision, thought it can induce some backlash. The other way of minimizing cogging is to skew the magnets on the rotor so that a radial line from the center of the rotor always intersects a magnet at least once. When using a motor without gearing, it is known as a direct drive motor. This allows for the best transfer of power to the load, and avoids any of the negative aspects of gearing previously mentioned. A feature in newer servo motors (including the Bodine models used in this thesis) is the use of an ironless stator, which eliminates iron saturation, a situation where the magnetic properities of the iron limit how much current can be applied to the windings. Inducing iron saturation too ofen will cause overheating and possibly damage the winding or magnets. With an ironless stator, rotor magnet skewing is not necessary, as the magnetic fields aren't influenced by the material of the stator. Also, since the only mechanical connection between the shaft and the body is through the bearings, friction is very low (especialy when using ball bearings).
In high torque motors such as the ones used in this thesis, the rotor actually consists of two plates of permanet magnets sandwiching the stator, which allows for a major increase in torque. This feature only exists in axial flux motors, due to the design where the stator lies in between the rotors, whereas in radial flux servos, the rotor is completely enclosed by the stator. The majority of the heat dissipated from a servo motor comes from the stator, so its outside location adis in cooling. In fact, the main limiting fator in the power of a servo motor is the heat capacity of the stator and the armature windings.
Fasttobuy Servo Motor On Sale In this September
If you are interested in these servo motor, you can click this link: https://www.fasttobuy.com/specials.html
2016年8月31日星期三
The Advantages and Working of a Servo Motor
Servo control, which is known as "motion control" or "robotics" is used in industrial processes to move a specific load in a controlled fashion. These systems can utilize either pneumatic, hydraulic, or electromechanical actuation technology. The choice of the actuator type (i.e. the device that provides the power to move the load) is based on power, speed, precision, and cost requirements. Electromechanical systems are typically used in high precision, low to medium power, and high-speed applications. These systems are flexible, efficient, and cost-effective. Servo Motors are the actuators used in electromechanical systems. Through the interaction of electromagnetic fields, they generate power.
Servo Motor Advantages
Servo motors with related controls provide very precise and repeatable control of both position and velocity, and its various feedback parameters allow users to closely monitor the dispensing process and detect any abnormalities before they can become major problems. There are three main advantages to servo drive technology in adhesive and sealant dispensing equipment:
1. Servo drive motors allows you to have preset, multi-segment shot profiles, with each segment having its own material volume and flow rate, and with the ability to smoothly blend the motion of each segment into the next one in the profile. The user can then select from among these preset profiles before initiating the dispense cycle.
2. Servo technology also allows you to continuously vary the material flow rate during the dispense cycle based upon a command reference from the process control. This allows the user to either apply a continuous bead of material with varying bead widths, or conversely, to maintain the same bead width despite changes in the applicator's linear speed, for example when a robot slows down to negotiate a complex curve.
3. A major advantage to servo control is its ability to reliably maintain the commanded volumetric flow rate of material despite changes in the physical conditions of the dispensing system or its environment. Examples of these types of changes are variations in material viscosity, and therefore in the back pressure it generates during the dispense cycle, due to such things as variations in ambient temperature or differences in batches of material; variations in the plant utilities supplied to the dispensing equipment, such as air pressure or electrical voltage; and load changes due to physical wear on the dispensing equipment as it ages. The servo drive simply increases or decreases the amount of current it supplies to the motor as required to maintain the commanded material flow rate, up to the current limits of the drive. If those limits are ever exceeded, the drive generates a fault and stops the cycle, which prevents the customer from unknowingly making out of spec parts.
Working of a Servo Motor
Servo motors are utilized to control position and speed very precisely, but in an easy case, only position may be controlled. Mechanical position of the shaft can be sensed by using a potentiometer, which is coupled with the motor shaft through gears. The current position of the shaft is converted into electrical signal by the potentiometer, and the compared with the command input signal. In modern servo motors, electronic encoders or sensors are used to sense the position of the shaft.
Command input is given according to the required position of the shaft. If the feedback signal differs from the given input, an error signal is generated. This error signal is then amplified and applied as the input to the motor, which causes the motor to rotate. And when the shaft reaches to the required position, error signal becomes zero, and hence the motor stays standstill holding the position.
The command input is given in the form of electrical pulses. As the actual input applied to the motor is the difference between feedback signal (current position) and applied signal (required position), speed of the motor is proportional to the difference between the current position and the required position. The amount of power required by the motor is proportional to the distance it needs to travel.
Servo Motor Advantages
Servo motors with related controls provide very precise and repeatable control of both position and velocity, and its various feedback parameters allow users to closely monitor the dispensing process and detect any abnormalities before they can become major problems. There are three main advantages to servo drive technology in adhesive and sealant dispensing equipment:
1. Servo drive motors allows you to have preset, multi-segment shot profiles, with each segment having its own material volume and flow rate, and with the ability to smoothly blend the motion of each segment into the next one in the profile. The user can then select from among these preset profiles before initiating the dispense cycle.
2. Servo technology also allows you to continuously vary the material flow rate during the dispense cycle based upon a command reference from the process control. This allows the user to either apply a continuous bead of material with varying bead widths, or conversely, to maintain the same bead width despite changes in the applicator's linear speed, for example when a robot slows down to negotiate a complex curve.
3. A major advantage to servo control is its ability to reliably maintain the commanded volumetric flow rate of material despite changes in the physical conditions of the dispensing system or its environment. Examples of these types of changes are variations in material viscosity, and therefore in the back pressure it generates during the dispense cycle, due to such things as variations in ambient temperature or differences in batches of material; variations in the plant utilities supplied to the dispensing equipment, such as air pressure or electrical voltage; and load changes due to physical wear on the dispensing equipment as it ages. The servo drive simply increases or decreases the amount of current it supplies to the motor as required to maintain the commanded material flow rate, up to the current limits of the drive. If those limits are ever exceeded, the drive generates a fault and stops the cycle, which prevents the customer from unknowingly making out of spec parts.
Working of a Servo Motor
Servo motors are utilized to control position and speed very precisely, but in an easy case, only position may be controlled. Mechanical position of the shaft can be sensed by using a potentiometer, which is coupled with the motor shaft through gears. The current position of the shaft is converted into electrical signal by the potentiometer, and the compared with the command input signal. In modern servo motors, electronic encoders or sensors are used to sense the position of the shaft.
Command input is given according to the required position of the shaft. If the feedback signal differs from the given input, an error signal is generated. This error signal is then amplified and applied as the input to the motor, which causes the motor to rotate. And when the shaft reaches to the required position, error signal becomes zero, and hence the motor stays standstill holding the position.
The command input is given in the form of electrical pulses. As the actual input applied to the motor is the difference between feedback signal (current position) and applied signal (required position), speed of the motor is proportional to the difference between the current position and the required position. The amount of power required by the motor is proportional to the distance it needs to travel.
2016年8月25日星期四
Connecting a Servo Motor
Servo motors typically have three wires. The power wire, usually red, is connected to teh power rail. The ground wire, ususally black or brown, is connected to the ground rail. The third wire, usually yellow or oragne, is the signal wire and is connected directly to a digital pin on the Arduino. The Arduino can normally directly supply power to a servo motor, but when using serveral servo motors, you ned to separate the Arduino power supply to the servo power supply to avoid brown outs. Servo motors, even if they do not always act like typical motors, still have a small motor inside and can draw large amounts of current, far more than what the ATmega can deliver.

Before using servo motors, you must import the Servo library. You can do this either by importing the library. You can do this either by importing the library through the Arduino IDE menu (Sketch Import Library servo) or by manually typing:
#include (servo.h)
In your software, you must first creat a new servo object before issuing instructions. You must create one object per servo motor (or group of servo motors) to contorl.
Servo frontWheels;
Servo rearWheels;
To tell the Arduino which pins the servo motors are connected to, call attach(), specifying the pin, and optionally, specifying the minimum and maximum pulse size.
servo attach (pin)
servo attach (pin, min, max)
By default, Arduino uses 544 microseconds as the minimum pulse length (equivalent to 0 degrees) and 2,400 microseconds as the maximum pulse width (equivalent to 180 degrees.) If your servo motor has different settings for a maximum and minimum pulse, you can change the values in attch () by specifying the duration in microseconds. For example, a servo motor that uses a 1 millisecond minimum and 2 millisecond maximum can be configured like this:
servo.attach (pin, 1000, 2000);
From then on, the Arduino automatically calculates the length of the pulse according to the wanted angle but will not issue commands until a function specifically orders the servo motor to move.

Before using servo motors, you must import the Servo library. You can do this either by importing the library. You can do this either by importing the library through the Arduino IDE menu (Sketch Import Library servo) or by manually typing:
#include (servo.h)
In your software, you must first creat a new servo object before issuing instructions. You must create one object per servo motor (or group of servo motors) to contorl.
Servo frontWheels;
Servo rearWheels;
To tell the Arduino which pins the servo motors are connected to, call attach(), specifying the pin, and optionally, specifying the minimum and maximum pulse size.
servo attach (pin)
servo attach (pin, min, max)
By default, Arduino uses 544 microseconds as the minimum pulse length (equivalent to 0 degrees) and 2,400 microseconds as the maximum pulse width (equivalent to 180 degrees.) If your servo motor has different settings for a maximum and minimum pulse, you can change the values in attch () by specifying the duration in microseconds. For example, a servo motor that uses a 1 millisecond minimum and 2 millisecond maximum can be configured like this:
servo.attach (pin, 1000, 2000);
From then on, the Arduino automatically calculates the length of the pulse according to the wanted angle but will not issue commands until a function specifically orders the servo motor to move.
2016年8月23日星期二
How to Wire Your Stepper
A stepper motor can come with assortment of wire configurations. The type of motor you’ve selected will determine the wire setup. Most commonly stepper motors come with four, five, six, or eight wires.
To begin, if your stepper motor only has four wires, this means it can only be used with a bipolar driver. You will notice each of the two phase windings has a pair of wires, use your meter to identify the wires.
4 Wire Stepper Motors
W numerous motors make the most of 6- and 8-wire configurations, the majority of bipolar (1 winding per phase) stepper motors offer 4 wires to connect towards the motor windings. A fundamental 4-wire stepper motor is shown in Figure 1. Connecting this motor kind is extremely simple and merely demands connecting the A and A' results in the corresponding phase outputs in your motor drive.
There's not a lot detailing right here. The 4 wire stepper denotes a single feasible configuration and that's of a bipolar stepper motor. We don't have to bore us with particulars like whether or not this motor is variably reluctance, permanent magnet or hybrid as that only relates to building. What we have to understand is the fact that two wires are for PHASE A and also the other two wires are for PHASE B. Which 1 is PHASE A and which 1 is PHASE B is type of arbitrary.
If you have the motor datasheet then you know which wires represent which. But if you do not have this document, just do a quick continuity test and determine which two wires are connected together through an inductor. You can also use a simple BACK EMF test in which you short two leads together. If it is harder to move the rotor, then those two wires form one of the phases. If the rotor moves as easy as with no wires crossed over, then those two wires are not connected through a winding. Keep on going until you find both phases.
The Five Wire Stepper
This motor is also equally easy to deal with as it can only be wired as an unipolar stepper motor. There is really no way to use this motor in a bipolar configuration as all the center taps have been shorted together. Do note this motor style is quite rare. I think these motors were more common a few years ago when unipolar motors were much more cost effective. Today, however, since driving bipolar motors is not a superbly expensive endeavor, the five wire stepper motor is not as common as it used to be. Instead, the six wire stepper motor has replaced the five wire stepper motor because of what we will see next. If you do happen to get your hands on a five wire stepper motor, here is how you wire it:
The Six Wire Stepper
We can now start to complicate things. As it turns out, the six wire stepper is optimized to operate as a unipolar stepper motor but it is rather doable to use it as a bipolar stepper motor as well. The trick, however, is that there are multiple ways of wiring the motor as bipolar and it all depends on what you will want to achieve. For example, do you want speed, or do you want torque? Maybe you want both? Well, I can only promise one or the other by utilizing conventional drive technology. If you want both (torque and speed) you will need to resort to some highly advanced drive technology, which although available out there, is not in the$5.00 range.
So lets first see how to wire the six wire stepper as a unipolar motor:
A bipolar driver will require you use only one end wire and one center tap of each winding. With a five wire stepper motor the wire setup is very similar to the six wire driver, the main difference being the center taps are connected together internally, bringing it out as one wire. This will make the motor only function as a unipolar driver. Also, the windings will be impossible to identify without trial and error, the best you can do is try to identify the center tap wire since it has half the resistance.
Finally there is the eight wire stepper motor, which is much like the six wire. The difference being that the two phases are split into two separate windings. When this is done it allows for the stepper motor to be connected as a unipolar motor, as well as three different bipolar combinations.
To begin, if your stepper motor only has four wires, this means it can only be used with a bipolar driver. You will notice each of the two phase windings has a pair of wires, use your meter to identify the wires.
4 Wire Stepper Motors
W numerous motors make the most of 6- and 8-wire configurations, the majority of bipolar (1 winding per phase) stepper motors offer 4 wires to connect towards the motor windings. A fundamental 4-wire stepper motor is shown in Figure 1. Connecting this motor kind is extremely simple and merely demands connecting the A and A' results in the corresponding phase outputs in your motor drive.
There's not a lot detailing right here. The 4 wire stepper denotes a single feasible configuration and that's of a bipolar stepper motor. We don't have to bore us with particulars like whether or not this motor is variably reluctance, permanent magnet or hybrid as that only relates to building. What we have to understand is the fact that two wires are for PHASE A and also the other two wires are for PHASE B. Which 1 is PHASE A and which 1 is PHASE B is type of arbitrary.
If you have the motor datasheet then you know which wires represent which. But if you do not have this document, just do a quick continuity test and determine which two wires are connected together through an inductor. You can also use a simple BACK EMF test in which you short two leads together. If it is harder to move the rotor, then those two wires form one of the phases. If the rotor moves as easy as with no wires crossed over, then those two wires are not connected through a winding. Keep on going until you find both phases.
The Five Wire Stepper
This motor is also equally easy to deal with as it can only be wired as an unipolar stepper motor. There is really no way to use this motor in a bipolar configuration as all the center taps have been shorted together. Do note this motor style is quite rare. I think these motors were more common a few years ago when unipolar motors were much more cost effective. Today, however, since driving bipolar motors is not a superbly expensive endeavor, the five wire stepper motor is not as common as it used to be. Instead, the six wire stepper motor has replaced the five wire stepper motor because of what we will see next. If you do happen to get your hands on a five wire stepper motor, here is how you wire it:
The Six Wire Stepper
We can now start to complicate things. As it turns out, the six wire stepper is optimized to operate as a unipolar stepper motor but it is rather doable to use it as a bipolar stepper motor as well. The trick, however, is that there are multiple ways of wiring the motor as bipolar and it all depends on what you will want to achieve. For example, do you want speed, or do you want torque? Maybe you want both? Well, I can only promise one or the other by utilizing conventional drive technology. If you want both (torque and speed) you will need to resort to some highly advanced drive technology, which although available out there, is not in the$5.00 range.
So lets first see how to wire the six wire stepper as a unipolar motor:
A bipolar driver will require you use only one end wire and one center tap of each winding. With a five wire stepper motor the wire setup is very similar to the six wire driver, the main difference being the center taps are connected together internally, bringing it out as one wire. This will make the motor only function as a unipolar driver. Also, the windings will be impossible to identify without trial and error, the best you can do is try to identify the center tap wire since it has half the resistance.
Finally there is the eight wire stepper motor, which is much like the six wire. The difference being that the two phases are split into two separate windings. When this is done it allows for the stepper motor to be connected as a unipolar motor, as well as three different bipolar combinations.
2016年8月18日星期四
Gearmotor selection/tech questions - DIY 3D printer
Gears, the universal symbol of productivity, have been a major cog in industry for hundreds of years. Before electromagnetic rotating machines were even a glimmer in Michael Faraday's eyes, there were gears.
Early gears had been produced from wood with cylindrical pegs for cogs. They had been frequently lubricated with animal fat, vegetable oils, as well as water. Gears had been utilized then for exactly the same factors they're now - simply because of their force multiplying properties. You’d discover them on ships (hoisting anchors), in catapults (tensioning fly arms), and on a number of machinery powered by wind and water wheels.
The choice of motor will depend largely on what software interface you plan to use. If you want to use pre-made software, then you might want to stick to the type of actuator they use/ suggest: it might be a stepper motor, servo or DC gear motor + encoder.
If you plan to make your own software interface, then using the same type of actuator throughout the machine has its advantages - and we'd suggest you again use a stepper motor.
If you really wanted to use a DC gear motor with encoder, you'd need a DC motor controller (serial or PWM) and connect the encoder output to the microcontroller. You would then need to program the microcontroller separately from the software you use to slice the part. It's quite involved. The Arduino would provide the 5V power for the encoder and read the states of the onboard IR sensors.
Gear types
There are many types of gears available today, each with specific advantages and limitations. Topping the list — at least for big jobs — are worm, spur, and helical gears.
Spur gears are compact as well as efficient, but they tend to be noisy and don’t always handle shock as well as worm gears. They can achieve about 10:1 ratio per stage.
Worm gears are relatively inexpensive, achieve high ratios in a single gear set (up to 100:1), and are available in right-angle configurations. They also run quietly and tolerate high shock loads. However, they are less efficient than other forms of gearing.
Spur gears by contrast are much more most likely to create noise, much less tolerant of shock in comparison to worm gears, and slightly much more costly. Around the plus side, they're compact, effective, and accessible in parallel-shaft arrangements. They're also simple to discover simply because numerous producers create them. Spur gear ratios are usually ten:1 per stage.
Helical gears are similar to spur gears, but they have angled teeth. Because helical gears have more tooth contact area than spur gears, pound for pound they can carry heavier loads, though not quite as efficiently. They are somewhat more expensive as well and, depending on the configuration, may produce thrust loading on the bearings. Versatility is a plus, however, as helicals can be used on non-parallel, even perpendicular, shafts, achieving a 10:1 ratio per stage.
Early gears had been produced from wood with cylindrical pegs for cogs. They had been frequently lubricated with animal fat, vegetable oils, as well as water. Gears had been utilized then for exactly the same factors they're now - simply because of their force multiplying properties. You’d discover them on ships (hoisting anchors), in catapults (tensioning fly arms), and on a number of machinery powered by wind and water wheels.
The choice of motor will depend largely on what software interface you plan to use. If you want to use pre-made software, then you might want to stick to the type of actuator they use/ suggest: it might be a stepper motor, servo or DC gear motor + encoder.
If you plan to make your own software interface, then using the same type of actuator throughout the machine has its advantages - and we'd suggest you again use a stepper motor.
If you really wanted to use a DC gear motor with encoder, you'd need a DC motor controller (serial or PWM) and connect the encoder output to the microcontroller. You would then need to program the microcontroller separately from the software you use to slice the part. It's quite involved. The Arduino would provide the 5V power for the encoder and read the states of the onboard IR sensors.
Gear types
There are many types of gears available today, each with specific advantages and limitations. Topping the list — at least for big jobs — are worm, spur, and helical gears.
Spur gears are compact as well as efficient, but they tend to be noisy and don’t always handle shock as well as worm gears. They can achieve about 10:1 ratio per stage.
Worm gears are relatively inexpensive, achieve high ratios in a single gear set (up to 100:1), and are available in right-angle configurations. They also run quietly and tolerate high shock loads. However, they are less efficient than other forms of gearing.
Spur gears by contrast are much more most likely to create noise, much less tolerant of shock in comparison to worm gears, and slightly much more costly. Around the plus side, they're compact, effective, and accessible in parallel-shaft arrangements. They're also simple to discover simply because numerous producers create them. Spur gear ratios are usually ten:1 per stage.
Helical gears are similar to spur gears, but they have angled teeth. Because helical gears have more tooth contact area than spur gears, pound for pound they can carry heavier loads, though not quite as efficiently. They are somewhat more expensive as well and, depending on the configuration, may produce thrust loading on the bearings. Versatility is a plus, however, as helicals can be used on non-parallel, even perpendicular, shafts, achieving a 10:1 ratio per stage.
2016年8月15日星期一
Types of Stepper Motor and Their Significances
A stepper motor is definitely an electromechanical device that induces mechanical movements by converting electrical pulses. It's driven by digital pulses rather of constantly applied voltage, and it could step or rotate in fixed angular increments. Stepper motors are usually utilized in applications that need position manage. They're assumed to adhere to digital directions when utilized inside a stepper motor method style. They are classified as open-loop systems due to their lack of feedback to keep control of the position. Stepper motors can be classified into three basic types:
Variable reluctance stepper motor:
The VR stepper motor is characterized by the fact that there is no permanent magnet either on the rotor or the stator. The construction of a 3-phase VR stepper motor is shown in figure.
The stator is produced up of silicon steel stamping s with inward projected even or odd quantity of poles or teeth (generally the amount of poles of stator is definitely an even quantity). Every and each stator pole carries a field coil or thrilling coil. In case of even quantity of poles the thrilling coils of opposite poles are connected in series. The two coils are connected such that their MMF get added. The mixture of two coils is recognized as phase winding.
The rotor is also made up of silicon steel stamping s with outward projected poles and it does not have any electrical winding. The number rotor poles should not be equal to the number of stator poles to have self starting capability and bi-directional rotation. The width of the rotor teeth should be equal to the width of stator teeth.
Permanent magnet stepper motor:
Permanent Magnet (PM) motors use permanent magnet rotors and are commanded by electrical pulses. They are widely used in printers, copies, and scanners, among other applications. They are also used to operate valves in household water and gas systems as well as drive actuators in automotive applications.
One of the main benefits of the PM stepper motor is that, in addition to being electronically commutated like a brushless DC motor or any other type of stepper motor, the PM stepper motor requires no “teeth” as are typically found in the variable reluctance (VR) stepper motor. This makes the permanent magnet stepper an extremely popular choice for many motor applications.
Hybrid Stepper motors:
Hybrid stepper motors provide excellent performance in areas of torque, speed, and step resolution. Typically, step angles for a hybrid stepper motor range from 200 to 400 steps per revolution. This type of motor provides a combination of the best features available on both the PM and VR types of stepper motors. Hybrid stepper motors enhance the performance in terms of torque, speed, and step resolution, so they are useful in applications that require high stepping speeds for operation. They come in step angles designed at 0.9 degrees, 1.8 degrees (commonly used), 3.6 degrees, and 4.5 degrees.
We have excellent teams in manufacturing and researching motors., and with rich experience in this field, we can solve the actual using problems for customers. Our products are highly commended by customers because of its easy operation, long using life, stable performance, low failure rate and high technical content.
About Fasttobuy:
Our products are widely applied in printing equipment, engraving machine textile machine, computer external application equipment, medical instruments, stage light equipment, robot, NC machine tool and other automatic controlling system. Our main products include NEMA8, NEMA11, MENA14, MENA15, NEMA17, NEMA23, NEMA24, NEMA34 and NEMA43 series hybrid stepper motor.
Variable reluctance stepper motor:
The VR stepper motor is characterized by the fact that there is no permanent magnet either on the rotor or the stator. The construction of a 3-phase VR stepper motor is shown in figure.
The stator is produced up of silicon steel stamping s with inward projected even or odd quantity of poles or teeth (generally the amount of poles of stator is definitely an even quantity). Every and each stator pole carries a field coil or thrilling coil. In case of even quantity of poles the thrilling coils of opposite poles are connected in series. The two coils are connected such that their MMF get added. The mixture of two coils is recognized as phase winding.
The rotor is also made up of silicon steel stamping s with outward projected poles and it does not have any electrical winding. The number rotor poles should not be equal to the number of stator poles to have self starting capability and bi-directional rotation. The width of the rotor teeth should be equal to the width of stator teeth.
Permanent magnet stepper motor:
Permanent Magnet (PM) motors use permanent magnet rotors and are commanded by electrical pulses. They are widely used in printers, copies, and scanners, among other applications. They are also used to operate valves in household water and gas systems as well as drive actuators in automotive applications.
One of the main benefits of the PM stepper motor is that, in addition to being electronically commutated like a brushless DC motor or any other type of stepper motor, the PM stepper motor requires no “teeth” as are typically found in the variable reluctance (VR) stepper motor. This makes the permanent magnet stepper an extremely popular choice for many motor applications.
Hybrid Stepper motors:
Hybrid stepper motors provide excellent performance in areas of torque, speed, and step resolution. Typically, step angles for a hybrid stepper motor range from 200 to 400 steps per revolution. This type of motor provides a combination of the best features available on both the PM and VR types of stepper motors. Hybrid stepper motors enhance the performance in terms of torque, speed, and step resolution, so they are useful in applications that require high stepping speeds for operation. They come in step angles designed at 0.9 degrees, 1.8 degrees (commonly used), 3.6 degrees, and 4.5 degrees.
We have excellent teams in manufacturing and researching motors., and with rich experience in this field, we can solve the actual using problems for customers. Our products are highly commended by customers because of its easy operation, long using life, stable performance, low failure rate and high technical content.
About Fasttobuy:
Our products are widely applied in printing equipment, engraving machine textile machine, computer external application equipment, medical instruments, stage light equipment, robot, NC machine tool and other automatic controlling system. Our main products include NEMA8, NEMA11, MENA14, MENA15, NEMA17, NEMA23, NEMA24, NEMA34 and NEMA43 series hybrid stepper motor.
2016年8月12日星期五
How to Select the Right Gearmotor
Gear motors are crucial elements of any systems they drive. They're by their extremely nature the muscle that moves your machinery. That tends to make your gear motor supplier an integral a part of your provide chain. That stated, does your present Gear reduction motors supplier provide you with the tools and assistance that you simply have to rapidly, effortlessly, and reliably do your job? Make certain your supplier can answer these concerns to address the discomfort points that numerous gear motor clients like your self frequently encounter. If they can?ˉt, it might be time for you to appear someplace else.
Because the motor or gearmotor choice procedure starts, the designer should collect the relevant technical and industrial specifications. This initial step is frequently overlooked, however it is really a crucial element within the style procedure. The gathered style inputs info will then be utilized within the choice procedure and can dictate the perfect motor for the application. Failure to collect the correct inputs can lead the designer down an untended path. Because of this, it's useful to make use of the Application Checklist (Table two) when creating the motor specification. These parameters, together with some project particular specifications, will probably be useful when navigating the choice procedure.
Next, the designer should think about what kind of motor technologies very best suits the intended application. Utilizing the style inputs, the Motors Fast Reference Guide (Table three) may be utilized as a choice matrix within the initial step from the choice procedure. This reference guide particulars 4 typical motor kinds and offers common info to think about when choosing every motor. Simply because every application has its personal distinctive traits, it's essential to figure out which from the parameters (e.g. horsepower, efficiency, life, beginning torque or noise ratings) are most significant towards the application below consideration. Throughout the motor choice procedure, by taking a look at the needed speed and torque from the application, it ought to turn out to be evident towards the designer when the motor selected demands a gearbox to meet the essential specifications. If a dc worm gear motor is essential for the application, an additional degree of complexity will probably be added and a number of extra criteria require to become evaluated.
Conceptually, motors and gearboxes can be mixed and matched as needed to best fit the application, but in the end, the complete gearmotor is the driving factor. There are a number of motors and gearbox types that can be combined; for example, the right angle worm, planetary and parallel shaft gearboxes can be combined with permanent magnet DC, AC induction, or brushless DC motors. Though there are a vast number of different motors and gearboxes combinations available, not just any one will work for the application. There will be certain combinations that will be more efficient and cost-effective than others. Knowing the application and having accurate ratings for the motor and gearbox is the foundation for successfully integrating the gearmotor into the system.
Some tips for you:
1. Knowing the Application Requirements
Knowing the specific requirements of your application will help you determine if you need a DC or AC gear motor, and the specific type. Such requirements include:
Environment: Application and ambient temperature, and ingress protection (IP) rating
General requirements: Envelope size, side and overhung loads, lubrication type, mounting orientation and mounting type
Input power source: maximum current (amps), frequency (hertz), voltage and control type
Gear motor performance: Speed, torque, duty cycle, horsepower and starting and stall torque
Gear motor specifications: Size, weight, desired noise level, desired maintenance level and life expectancy
2. Choosing the Right Motor
Use the list of application requirements that you gathered and compare them to the specifications of the DC and AC gear motors of interest, such as universal, brushless DC, AC induction and permanent magnet motors. In lieu of a pre-engineered motor, you may find that selecting a gearbox and motor separately may be best for your application.
3. Matching Performance Curves, Pull-Up Torque and Yield Strength to the Gear Motor
The proper torque and speed is important when choosing a gear motor. Use a manufacturer’s or vendor’s overall performance curves concerning torque, speed and efficiency to locate a gear motor that matches your requirements. Following discovering a couple of overall performance curves, yield strengths and pull-up torques that match the application’s requirements, examine the style limitations, like thermal traits, to narrow down the options.
By accounting for all of those elements inside your calculations when selecting a motor and gear ratio, you'll make sure that your robot functions as you intend the very first time about. The instance issue in the finish of this tutorial will demonstrate how you can undergo the procedure of creating these calculations.
Related Products:
http://www.fasttobuy.com/50rpm-dc24v-069nm-7kgcm-turbo-worm-gear-motor-gw31zy-diy-robot_p35783.html
Because the motor or gearmotor choice procedure starts, the designer should collect the relevant technical and industrial specifications. This initial step is frequently overlooked, however it is really a crucial element within the style procedure. The gathered style inputs info will then be utilized within the choice procedure and can dictate the perfect motor for the application. Failure to collect the correct inputs can lead the designer down an untended path. Because of this, it's useful to make use of the Application Checklist (Table two) when creating the motor specification. These parameters, together with some project particular specifications, will probably be useful when navigating the choice procedure.
Next, the designer should think about what kind of motor technologies very best suits the intended application. Utilizing the style inputs, the Motors Fast Reference Guide (Table three) may be utilized as a choice matrix within the initial step from the choice procedure. This reference guide particulars 4 typical motor kinds and offers common info to think about when choosing every motor. Simply because every application has its personal distinctive traits, it's essential to figure out which from the parameters (e.g. horsepower, efficiency, life, beginning torque or noise ratings) are most significant towards the application below consideration. Throughout the motor choice procedure, by taking a look at the needed speed and torque from the application, it ought to turn out to be evident towards the designer when the motor selected demands a gearbox to meet the essential specifications. If a dc worm gear motor is essential for the application, an additional degree of complexity will probably be added and a number of extra criteria require to become evaluated.
Conceptually, motors and gearboxes can be mixed and matched as needed to best fit the application, but in the end, the complete gearmotor is the driving factor. There are a number of motors and gearbox types that can be combined; for example, the right angle worm, planetary and parallel shaft gearboxes can be combined with permanent magnet DC, AC induction, or brushless DC motors. Though there are a vast number of different motors and gearboxes combinations available, not just any one will work for the application. There will be certain combinations that will be more efficient and cost-effective than others. Knowing the application and having accurate ratings for the motor and gearbox is the foundation for successfully integrating the gearmotor into the system.
Some tips for you:
1. Knowing the Application Requirements
Knowing the specific requirements of your application will help you determine if you need a DC or AC gear motor, and the specific type. Such requirements include:
Environment: Application and ambient temperature, and ingress protection (IP) rating
General requirements: Envelope size, side and overhung loads, lubrication type, mounting orientation and mounting type
Input power source: maximum current (amps), frequency (hertz), voltage and control type
Gear motor performance: Speed, torque, duty cycle, horsepower and starting and stall torque
Gear motor specifications: Size, weight, desired noise level, desired maintenance level and life expectancy
2. Choosing the Right Motor
Use the list of application requirements that you gathered and compare them to the specifications of the DC and AC gear motors of interest, such as universal, brushless DC, AC induction and permanent magnet motors. In lieu of a pre-engineered motor, you may find that selecting a gearbox and motor separately may be best for your application.
3. Matching Performance Curves, Pull-Up Torque and Yield Strength to the Gear Motor
The proper torque and speed is important when choosing a gear motor. Use a manufacturer’s or vendor’s overall performance curves concerning torque, speed and efficiency to locate a gear motor that matches your requirements. Following discovering a couple of overall performance curves, yield strengths and pull-up torques that match the application’s requirements, examine the style limitations, like thermal traits, to narrow down the options.
By accounting for all of those elements inside your calculations when selecting a motor and gear ratio, you'll make sure that your robot functions as you intend the very first time about. The instance issue in the finish of this tutorial will demonstrate how you can undergo the procedure of creating these calculations.
Related Products:
http://www.fasttobuy.com/50rpm-dc24v-069nm-7kgcm-turbo-worm-gear-motor-gw31zy-diy-robot_p35783.html
2016年8月9日星期二
Servo Motor Control with AdndroiDAQ
Servo motors are common motion control actuators that are used in robotics, radio controlled devices, 3D printers, and other motion drive systems. Using servo motors with AndroiDAQ is easy. This article contains a brief history of the servo motor, some basic operational background for servo motors, and how to connect and use a servo motor with the AndroiDAQ data acquisition and control module.
The steam engine governor is considered to be the first servo mechanism using a powered feedback system. Its first recorded use was in 1868, by JJL Farcot, who described steam engines and hydraulics for use in steering a ship. Servo mechanisms are considered to be closed-loop systems, as the mechanism uses position feedback to control its motion and final position.
Solution
Use PWM to control the width of pulses to a servo motor to change its angle. Although this will work, the PWM generated is not completely stable, so there will be a little bit of jitter with the servo.
You should also power the servo from a separate 5V power supply because peaks in the load current are likely to crash or overload the Raspberry Pi.
To make this recipe, you will need:
5V servo motor (see “Miscellaneous”)
Breadboard and jumper wires (see “Prototyping Equipment”)
1kΩ resistor (see “Resistors and Capacitors”)
5V 1A power supply or 4.8V battery pack (see “Miscellaneous”)
The breadboard layout for this is shown in Figure 5-1.
The 1kΩ resistor is not essential, but it does protect the GPIO pin from unexpectedly high currents in the control signal, which could occur if a fault developed on the servo.
The leads of the servo may not be the same as the colors indicated in Figure 5-2. It is common for the 5V wire to be red, the ground brown, and the control lead orange.
You can, if you prefer, power the servo from a battery pack rather than a power supply. Using a four-cell AA battery holder with rechargeable batteries will provide around 4.8V and work well with a servo. Using four alkali AA cells to provide 6V will be fine for many servos, but check the datasheet of your servo to make sure it is OK with 6V.
The user interface for setting the angle of the servo is based on the gui_slider.py program intended for controlling the brightness of an LED (“Controlling the Brightness of an LED”). However, you can modify it so that the slider sets the angle, between 0 and 180 degrees (Figure 5-2).
Open an editor (nano or IDLE) and paste in the following code. As with all the program examples in this book, you can also download the program from the Code section of the Raspberry Pi Cookbook website, where it is called servo.py.
Note that this program uses a graphical user interface, so you cannot run it from SSH.
You must run it from the windowing environment on the Pi itself or via remote control using VNC (“Controlling the Pi Remotely with VNC”). You also need to run it as superuser, so run it with the command sudo python servo.py:
from Tkinter import *
import RPi.GPIO as GPIO
import time
GPIO.setmode(GPIO.BCM)
GPIO.setup(18, GPIO.OUT)
pwm = GPIO.PWM(18, 100)
pwm.start(5)
class App:
def __init__(self, master):
frame = Frame(master)
frame.pack()
scale = Scale(frame, from_=0, to=180,
orient=HORIZONTAL, command=self.update)
scale.grid(row=0)
def update(self, angle):
duty = float(angle) / 10.0 + 2.5
pwm.ChangeDutyCycle(duty)
root = Tk()
root.wm_title('Servo Control')
app = App(root)
root.geometry("200x50+0+0")
root.mainloop()
A Servo Motor consists of three major parts: a motor, a controller circuit, and a feedback system, which usually consists of a potentiometer which is connected to the motor’s output shaft. The motor typically drives a set of gears, which turns the output shaft of the motor and the potentiometer simultaneously. The potentiometer’s measured resistance controls the output angle of the motor shaft. This resistance is fed into the servo controller circuit and when the controller circuit detects that the motor position is correct, it stops the servo motor. If the controller circuit detects that the angle is not correct, for whatever the motor it trying to control, it will turn the servo motor the correct direction until the angle is correct. Normally a servo motor is used to control an angular motion of between 0 and 180 degrees. They typically can not turn any further unless they are modified, due to a mechanical stop which is build onto the main output gear or the potentiometer itself. Servo motors are generally used as a high performance alternative to the stepper motor.
Servo motors are controlled by sending to the servo’s control wire a pulse train of variable width, or better, a pulse width modulated signal. This pulse train has to have specific parameters such as a minimum pulse, a maximum pulse, and a repetition rate. This signal is typically derived and sent to the servo control wire by a microcontroller such as the one on AndroiDAQ. The shaft angle of the servo is determined by the duration of the pulse train sent. Given the pulse train’s constraints of having a minimum pulse, a maximum pulse, and a repetition rate, a neutral position is defined. This neutral position is where the servo has exactly the same amount of potential rotation in the clockwise direction as it does in the counterclockwise direction. This neutral position is typically always around 1.5 milliseconds.
The steam engine governor is considered to be the first servo mechanism using a powered feedback system. Its first recorded use was in 1868, by JJL Farcot, who described steam engines and hydraulics for use in steering a ship. Servo mechanisms are considered to be closed-loop systems, as the mechanism uses position feedback to control its motion and final position.
Solution
Use PWM to control the width of pulses to a servo motor to change its angle. Although this will work, the PWM generated is not completely stable, so there will be a little bit of jitter with the servo.
You should also power the servo from a separate 5V power supply because peaks in the load current are likely to crash or overload the Raspberry Pi.
To make this recipe, you will need:
5V servo motor (see “Miscellaneous”)
Breadboard and jumper wires (see “Prototyping Equipment”)
1kΩ resistor (see “Resistors and Capacitors”)
5V 1A power supply or 4.8V battery pack (see “Miscellaneous”)
The breadboard layout for this is shown in Figure 5-1.
The 1kΩ resistor is not essential, but it does protect the GPIO pin from unexpectedly high currents in the control signal, which could occur if a fault developed on the servo.
The leads of the servo may not be the same as the colors indicated in Figure 5-2. It is common for the 5V wire to be red, the ground brown, and the control lead orange.
You can, if you prefer, power the servo from a battery pack rather than a power supply. Using a four-cell AA battery holder with rechargeable batteries will provide around 4.8V and work well with a servo. Using four alkali AA cells to provide 6V will be fine for many servos, but check the datasheet of your servo to make sure it is OK with 6V.
The user interface for setting the angle of the servo is based on the gui_slider.py program intended for controlling the brightness of an LED (“Controlling the Brightness of an LED”). However, you can modify it so that the slider sets the angle, between 0 and 180 degrees (Figure 5-2).
Open an editor (nano or IDLE) and paste in the following code. As with all the program examples in this book, you can also download the program from the Code section of the Raspberry Pi Cookbook website, where it is called servo.py.
Note that this program uses a graphical user interface, so you cannot run it from SSH.
You must run it from the windowing environment on the Pi itself or via remote control using VNC (“Controlling the Pi Remotely with VNC”). You also need to run it as superuser, so run it with the command sudo python servo.py:
from Tkinter import *
import RPi.GPIO as GPIO
import time
GPIO.setmode(GPIO.BCM)
GPIO.setup(18, GPIO.OUT)
pwm = GPIO.PWM(18, 100)
pwm.start(5)
class App:
def __init__(self, master):
frame = Frame(master)
frame.pack()
scale = Scale(frame, from_=0, to=180,
orient=HORIZONTAL, command=self.update)
scale.grid(row=0)
def update(self, angle):
duty = float(angle) / 10.0 + 2.5
pwm.ChangeDutyCycle(duty)
root = Tk()
root.wm_title('Servo Control')
app = App(root)
root.geometry("200x50+0+0")
root.mainloop()
A Servo Motor consists of three major parts: a motor, a controller circuit, and a feedback system, which usually consists of a potentiometer which is connected to the motor’s output shaft. The motor typically drives a set of gears, which turns the output shaft of the motor and the potentiometer simultaneously. The potentiometer’s measured resistance controls the output angle of the motor shaft. This resistance is fed into the servo controller circuit and when the controller circuit detects that the motor position is correct, it stops the servo motor. If the controller circuit detects that the angle is not correct, for whatever the motor it trying to control, it will turn the servo motor the correct direction until the angle is correct. Normally a servo motor is used to control an angular motion of between 0 and 180 degrees. They typically can not turn any further unless they are modified, due to a mechanical stop which is build onto the main output gear or the potentiometer itself. Servo motors are generally used as a high performance alternative to the stepper motor.
Servo motors are controlled by sending to the servo’s control wire a pulse train of variable width, or better, a pulse width modulated signal. This pulse train has to have specific parameters such as a minimum pulse, a maximum pulse, and a repetition rate. This signal is typically derived and sent to the servo control wire by a microcontroller such as the one on AndroiDAQ. The shaft angle of the servo is determined by the duration of the pulse train sent. Given the pulse train’s constraints of having a minimum pulse, a maximum pulse, and a repetition rate, a neutral position is defined. This neutral position is where the servo has exactly the same amount of potential rotation in the clockwise direction as it does in the counterclockwise direction. This neutral position is typically always around 1.5 milliseconds.
2016年8月3日星期三
Stepper Motor in Cllosed Loop Mode
Due to the limitations of open loop contorl, a closed loop control of stepper motors is used in practice. In a closed loop control, the input controller gets the information about the output through the feedback element. Hence the driver circuit receives the control signal which is based on the feedback information. So switching of the motor takes place by means of train of input pulses, which is generated on the basis of feedback from rotor. Such a switching of the motor is called as closed loop mode of operation of the stepper motor. The block diagram shown in the Fig.A.17 illustrates the closed loop operation of the stepper motor.
Let us consider a closed loop temperature control system. The temperature of the tank is required to be kept constant with the help of controlling the steam flow. There exists a valve whose position is controlled by a stepper motor, to control the steam flow. The actual temperature is sensed by using temperature sensor and feedback is given to the input controller. The input contorller has the reference information corresponding to the desired ideal temperature. It compare the feedback with this reference to generate the appropriate contorl signal. This control signal inturn is given to the driver circuit. The driver circuit control the excitation and logical sequence of the excitation of the phases. This drives the stepper motor and hence valve opening gets controlled appropriately so that steam flow gets controlled. This maintains the temperature of the tank constant. The logical operation of the system is illustrated in the block diagram shown in the Fig. A.18.
In a speed and position control systems, optical encoders coupled to the rotor shaft are used. Simlarly use of microprocessors as an input controller for better accuracy is very commen now a days. The Fig. A.19 shows the use of microprocessor in the closed loop control of the stepper motor.
What are the functionalities of these closed-loop stepper systems?
Closed-loop stepper with step-loss compensation will be the most typical kind of closed-loop stepper manage. The stepper drive operates as a micro-stepping drive and usually receives pulse and path commands to move towards the preferred position. An encoder tracks shaft or load position. If lost actions are detected, a compensation algorithm inserts extra actions to ensure that the motor shaft (or load) arrives in the preferred position. Usually, the stepper-motor drive has settings for two currents: The motor gets operating present when in motion and gets resting present when stopped.
In closed-loop stepper with load-position manage, the stepper drive operates as a typical microstepping drive and usually receives pulse and path commands to move towards the preferred position. The encoder (usually mounted around the load) monitors the load's position. The closed-loop algorithm dynamically tracks the load position and compensates all through the move profile. Usually, the motor gets operating present when in motion and gets resting present when stopped.
Closed-loop stepper servo manage treats the stepper motor like a high-pole-count brushless motor, turning it into a servomotor. A shaft-mounted encoder detects shaft position to figure out the correct present vector. A pulse and path interface might be provided within this kind of drive, however the position controller does not use actions to obtain towards the preferred position. Rather, closed-loop algorithms manage motor torque to servo the shaft into position utilizing a position manage loop (a PID loop for instance). Within this mode, the present setting is dynamic. The stepper drive delivers only the quantity of present required to move the motor shaft and load into position.
Let us consider a closed loop temperature control system. The temperature of the tank is required to be kept constant with the help of controlling the steam flow. There exists a valve whose position is controlled by a stepper motor, to control the steam flow. The actual temperature is sensed by using temperature sensor and feedback is given to the input controller. The input contorller has the reference information corresponding to the desired ideal temperature. It compare the feedback with this reference to generate the appropriate contorl signal. This control signal inturn is given to the driver circuit. The driver circuit control the excitation and logical sequence of the excitation of the phases. This drives the stepper motor and hence valve opening gets controlled appropriately so that steam flow gets controlled. This maintains the temperature of the tank constant. The logical operation of the system is illustrated in the block diagram shown in the Fig. A.18.
In a speed and position control systems, optical encoders coupled to the rotor shaft are used. Simlarly use of microprocessors as an input controller for better accuracy is very commen now a days. The Fig. A.19 shows the use of microprocessor in the closed loop control of the stepper motor.
What are the functionalities of these closed-loop stepper systems?
Closed-loop stepper with step-loss compensation will be the most typical kind of closed-loop stepper manage. The stepper drive operates as a micro-stepping drive and usually receives pulse and path commands to move towards the preferred position. An encoder tracks shaft or load position. If lost actions are detected, a compensation algorithm inserts extra actions to ensure that the motor shaft (or load) arrives in the preferred position. Usually, the stepper-motor drive has settings for two currents: The motor gets operating present when in motion and gets resting present when stopped.
In closed-loop stepper with load-position manage, the stepper drive operates as a typical microstepping drive and usually receives pulse and path commands to move towards the preferred position. The encoder (usually mounted around the load) monitors the load's position. The closed-loop algorithm dynamically tracks the load position and compensates all through the move profile. Usually, the motor gets operating present when in motion and gets resting present when stopped.
Closed-loop stepper servo manage treats the stepper motor like a high-pole-count brushless motor, turning it into a servomotor. A shaft-mounted encoder detects shaft position to figure out the correct present vector. A pulse and path interface might be provided within this kind of drive, however the position controller does not use actions to obtain towards the preferred position. Rather, closed-loop algorithms manage motor torque to servo the shaft into position utilizing a position manage loop (a PID loop for instance). Within this mode, the present setting is dynamic. The stepper drive delivers only the quantity of present required to move the motor shaft and load into position.
订阅:
博文 (Atom)